Hand Assistance for Paralysis Patients
Team Members
Shraddha Bhuwalka (DDS216020)
Arpit Khare (DDS216004)
Axat Srivastava (DDS216006)

Overview
The life of people with mobility issues, around the globe, has always been full of challenges. From day-to-today activities to personal healthcare, every task for them is challenged because of the lack of movement in some parts of their body. With this design exercise, We want to cater to a significant problem of theirs, which is, to help assist them with basic hand movement independently with the help of the device. Hand assistance for mobility issues existing in the market is mostly for rehab purposes to improve mobility through exercise. But there are few options to help them assist in the movement and help in the day-to-day activities. The concept is to make a hand assistance device with controls or motion/gesture sensors which can identify gestures trying to be performed and assist in performing them.
Inspiration
Many people must have encountered functionality or reduced mobility after an injury or a stroke. For example, someone had a stroke. The recovery, in this case, is delayed and might take years. Their finger won’t move as they should. We want to make a device or tool that would help and assist in the movement of fingers/hands.
Intent
Our intent for this project is to help people so that they can do the day-to-day activities by assisting with basic movements.
Objective
We shall try to achieve finger movement of the left hand. Target movements for the project:
Target movements for the project:
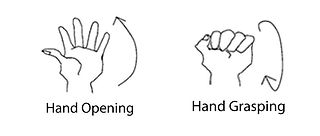

Conceptual Mechanism of Working of the Gripper
CONCEPTUAL FRAMEWORK
First making the mechanism for the assistant and then idealizing on the automation part.
AUTOMATION OF THE MOVEMENT
Using servo motor and adjusting its degree of rotation and speed as per the requirement.
The Shell Preparation
Taking the measurement of the phalanges, and carpals and drawing that is sunboard.
Cutting the shell of the gripper with sunboard and connecting the different parts with rubber bands, pins, toothpick and rubber tubes.
Then making the connecting wrist supports to enable the grip movement.
Frame Structure Design and Assembly
All the shells in a finger are connected together through a nylon string which then further connects to the shaft of the servo motor. When the motor’s shaft rotates 90 degrees, it pulls the string which ultimately forces the shells to contract. After reversing the switch, the shell takes their former position with the help of tension created by the rubber band behind them.
Programming and Electronics
A MG996R Servo Motor programmed and connected to Arduino Uno controlling the rotational angle and speed of the movement. It is connected to a switch which controls the motion in both directions.
List of Equipments & Materials used
1. Arduino Uno
2. MG996R Servo Motor
3. Jumper wires
4. Rubber bands
5. Styrofoam
6. Rubber tubes
7. 12V DV Battery
8. Nylon string
9. Toothpicks
10. Silicon solution and catalyst
Poster for the Project
